MIG/TIG welding
-
- ACVWSA Junkie
- Posts: 10784
- Joined: Wed Mar 07, 2007 10:41 am
- What model do you have?: none
- Location: Johannesburg
- Has thanked: 91 times
- Been thanked: 44 times
MIG/TIG welding
Which of these two types of welding is better?
Anyone know how much one of these machines costs?
Anyone know how much one of these machines costs?
If it's too low, you're too old 

-
- ACVWSA Junkie
- Posts: 10784
- Joined: Wed Mar 07, 2007 10:41 am
- What model do you have?: none
- Location: Johannesburg
- Has thanked: 91 times
- Been thanked: 44 times
-
- Carburettor
- Posts: 1924
- Joined: Tue Aug 07, 2007 3:27 pm
- What model do you have?: ZILTCH
- Facebook: www.facebook.com/brandon.gilson
- Location: Port Elizabeth
MIG/TIG WELDING
Hi Blitz,
The problem with both processes are that the volume x pressure of the bottles classify them as dangerous to use just like big oxy/accetelene sets so the bottles need to be registered to a owner and need to be inspected and certified as safe for further use on a regular basis. Thats why you never buy the bottles---only the content--- because Afrox or whoever stays legaly responsible for them. Small oxy/accetelene sets falls outside the volume x pressure cut of point so they are ok. (Ocupational and Health ACT )
So if you buy a big bottle from any one be assure its illegal.
You theoretically only rent the bottle and buy the content.
The rent is so high that it is not viable to go for any of these options unless you can make some money out of your welding.
The main difference between the two processes are;-
TIG produces a small area high concentration heat spot as against MIG with a lower heat imput wider area.
TIG will give you a deep penetration weld ie use for thick through thickness welds-- where MIG give a shallow penetration good for thin wall plate type materials.(les distortion)
Because TIG is a manual process the high heat distortion can be controled by stich welding or a lot of stop starts.
So------ both techniques can be learned, with TIG maybe easier because you determine the pace as you wish where MIG maybe more tricky --more variables to control at same time( settings on equipment need to be spot on)
For plate metal work MIG is the one but to have both would be very nice.
cheers
Baron
The problem with both processes are that the volume x pressure of the bottles classify them as dangerous to use just like big oxy/accetelene sets so the bottles need to be registered to a owner and need to be inspected and certified as safe for further use on a regular basis. Thats why you never buy the bottles---only the content--- because Afrox or whoever stays legaly responsible for them. Small oxy/accetelene sets falls outside the volume x pressure cut of point so they are ok. (Ocupational and Health ACT )
So if you buy a big bottle from any one be assure its illegal.
You theoretically only rent the bottle and buy the content.
The rent is so high that it is not viable to go for any of these options unless you can make some money out of your welding.
The main difference between the two processes are;-
TIG produces a small area high concentration heat spot as against MIG with a lower heat imput wider area.
TIG will give you a deep penetration weld ie use for thick through thickness welds-- where MIG give a shallow penetration good for thin wall plate type materials.(les distortion)
Because TIG is a manual process the high heat distortion can be controled by stich welding or a lot of stop starts.
So------ both techniques can be learned, with TIG maybe easier because you determine the pace as you wish where MIG maybe more tricky --more variables to control at same time( settings on equipment need to be spot on)
For plate metal work MIG is the one but to have both would be very nice.
cheers
Baron
-
- ACVWSA Junkie
- Posts: 10784
- Joined: Wed Mar 07, 2007 10:41 am
- What model do you have?: none
- Location: Johannesburg
- Has thanked: 91 times
- Been thanked: 44 times
-
- Carburettor
- Posts: 1924
- Joined: Tue Aug 07, 2007 3:27 pm
- What model do you have?: ZILTCH
- Facebook: www.facebook.com/brandon.gilson
- Location: Port Elizabeth
Contact Cromwell they have in there new 07-09 cataloge http://www.cromwell.co.za +- R3500 and it has small gas canisters B.A.B
Bad Ass ???


- IMPI
- Donor
- Posts: 1897
- Joined: Wed Sep 14, 2005 9:01 pm
- What model do you have?: sp2
- Location: Orkney Northwest province
- Has thanked: 1 time
- Been thanked: 78 times
I own a mig made by SIP in the uk at the time I bought it it was the cheapest mig in sa (se ad in car mag) it uses .6mm wire which is ideal for body work.
Tig welders need an absolutely clean surface for welds of good quality. this is not really possible on old car bodies. I dream of a tig but for welding heads etc.
The next easiest to use is oxy acetalene but too much heat causes warpage and is not reallly suitable for large flat panels such as doors etc.
Tig welders need an absolutely clean surface for welds of good quality. this is not really possible on old car bodies. I dream of a tig but for welding heads etc.
The next easiest to use is oxy acetalene but too much heat causes warpage and is not reallly suitable for large flat panels such as doors etc.
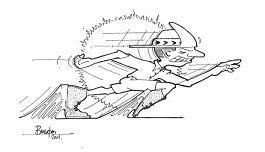
Who cares how it's done in California?

(018) 473-0186
-
- Oil Stain
- Posts: 160
- Joined: Thu Nov 08, 2007 1:07 am
- What model do you have?: Love Bug
- Location: Nazereth, Ethiopia But Stuck in Los Angeles at the moment....
If you plan on welding much Aluminum or Stainless, then TIG is the way to go. If you will be doing body work and steel like sheet metal and angle iron a 180 amp MIG welder is best. With the MIG welder you can also use what is called Flux Core wire. Lincolns is 211-MP. With this wire you dont need to use gas. It is the same type of wire that Professional welders use for building construction except they use bigger wire with a little different flux and more powerfull machines. You can find the MIG welders pretty cheap sometimes but you are better off with a Name brand like Lincoln or Miller. They will always have the consumable parts that are necessary. A Mig welder will be your best bet for youe VW work. I dont know what your voltage is but usually they are either 115 or 220 volts. Sometimes 370. If you have the 220 volt available at your house or shop, it is the best choice.
-
- Oil Stain
- Posts: 160
- Joined: Thu Nov 08, 2007 1:07 am
- What model do you have?: Love Bug
- Location: Nazereth, Ethiopia But Stuck in Los Angeles at the moment....
-
- Drive Train
- Posts: 3004
- Joined: Tue Feb 21, 2006 12:07 am
- What model do you have?: FUmobile
- Location: It doesn't matter.
- Been thanked: 1 time
Ok here is my take on it. And if I step on any toes, dont be offended. It is not personal.... I am purely commenting on the quotes because I personally feel they are not 100% correct
I have been working with MIG welders for over a year now, 9hrs a day(excluding hours put in at home on my welder). I have to disagree with Baron:
)
With a TIG welder, you do precision welding. Like HotRod chassis, aliminium heads, Stainless exhaust pipes, aliminium bicycle frames and the like. MIG welders is for 'bulk' work, but also sheet metal work. The biggest difference between TIG and MIG welding with regards to sheet metal work, is the 'flexibility' of the weld when worked on. With a MIG welder, the weld is harder and more brittle than with a TIG welder. If you weld two sheets with a MIG welder, and work it on an English wheel, or planishing hammer, chances are that the weld would develop a crack somewhere. However, if your TIG weld was not done properly, this would happen as well.
The reason I say that with a TIG welder, you can control your weld(process) MUCH more than with a MIG welder, is because of what I saw Ron Covell does with his TIG welder. And I challange ANYONE out there to make a video of it and send it to me personally(with their MIG welder)!!! Ron took two pieces of aliminium foil(yeah, those you wrap your sarnies in!!!) and seem-welded them together (without a filler rod obviously) with a TIG. It came out as one piece, not a single hole burned!! and to top it off, he tugged on it and it didnt tear!
Now before I go and lock myself up(before someone comes to tear me a new A-hole), I will give some good advice. STAY AWAY OF THESE MIG WELDERS(see pic below)

Notice those two small white switches? Those are your power settings. THEY SUCK!! Either not hot enough, or too hot. When welding panels, you either dont get decent enough penetration in your welds, OR, you burn a f-ing hole through your panel! TRUST ME, I have one gathering dust..... Then, I got me a decent one....

Here you can fine-tune your power settings vs. wire feed. Also, you got a 'timer' option. What this allows you to do is hold down the trigger to do a spot-weld, and after the preset time(in seconds), it will automatically stop welding. So you can for example set it to do a 5 second spot-weld. Much better machine, with WAY better results. I does come at a price though.
Oh yeah, and before I forget. Just as important... Go the extra stretch and get a contract for a gas bottle (normally Argon/CO2 mixture is used, but ATAL is just as good, and cheaper. BUT, it is not recommended to do S.Steel welding with ATAL gas). Forget that Core Flux wire. It SUCKS, especially when welding sheet metal/new panels on your restoration project!!!!!!
Ok, I think it is enough for now playing MR. I-know-it-all !!! And again, BAron, it is not personal, just my take on it
I have been working with MIG welders for over a year now, 9hrs a day(excluding hours put in at home on my welder). I have to disagree with Baron:
I would challenge ANYONE out there to show me just how easy it is to go and weld a 10mm plate with a TIG welder. Not that it cant be done, it is just going to take a LOT of effort/work and time. TIG welding needs a CLEAN, prepped area to weld. WIth a 10mm plate for example, you would need SEVERAL passes with a TIG welder to do a proper weld. And each time you do a pass, the heat(weld) would heat up the metal and bring out some of the natural 'impurities' in the metal.TIG will give you a deep penetration weld ie use for thick through thickness welds--
Contrary, MIG welding is used for THICK plates/metal. It is all in the way that the welding seem is prepped. However, on thick plates, several passes ALSO needs to be made with a MIG welder. At my work, we build big conveyor belts, and the chassis of these things often have metal in the region of 15-20mm. This is all MIG welded. On the other hand, with a decent MIG welder, properly adjusted, can successfully be used in sheet metal work. I.e. welding in new panels on your restoration project.where MIG give a shallow penetration good for thin wall plate type materials.(les distortion)
This comment is correct.Because TIG is a manual process the high heat distortion can be controled by stich welding or a lot of stop starts.
Incorrect. To do PROPER TIG welds, it takes a LOT of time and practice, and above all, PATIENCE. To get good penetration and a strong weld, you need to KNOW your machine well, and how to control it.So------ both techniques can be learned, with TIG maybe easier because you determine the pace as you wish
Again I disagree. Although the settings does need to be spot on, MIG welding is easy to learn. I would say that anyone that has got some DIY talent, can learn in a day how to do decent, clean and proper MIG welds. By no means would it always be 100% spot on, but you would be able to do good welds.where MIG maybe more tricky --more variables to control at same time( settings on equipment need to be spot on)
I would again say, for metal work that TIG is the one to have. But I agree, I would LOVE to have both. But the cost of a TIG welder prevents me from owning one(at least for now). It also has got draw backs, for example, you cant weld your new panels AND build a new fence for your garden with it, like you can do with a MIG welder!! (well, obviously you can, but it would be crawy to use a TIG welder to build a 30m fence with!!!For plate metal work MIG is the one but to have both would be very nice.

With a TIG welder, you do precision welding. Like HotRod chassis, aliminium heads, Stainless exhaust pipes, aliminium bicycle frames and the like. MIG welders is for 'bulk' work, but also sheet metal work. The biggest difference between TIG and MIG welding with regards to sheet metal work, is the 'flexibility' of the weld when worked on. With a MIG welder, the weld is harder and more brittle than with a TIG welder. If you weld two sheets with a MIG welder, and work it on an English wheel, or planishing hammer, chances are that the weld would develop a crack somewhere. However, if your TIG weld was not done properly, this would happen as well.
The reason I say that with a TIG welder, you can control your weld(process) MUCH more than with a MIG welder, is because of what I saw Ron Covell does with his TIG welder. And I challange ANYONE out there to make a video of it and send it to me personally(with their MIG welder)!!! Ron took two pieces of aliminium foil(yeah, those you wrap your sarnies in!!!) and seem-welded them together (without a filler rod obviously) with a TIG. It came out as one piece, not a single hole burned!! and to top it off, he tugged on it and it didnt tear!

Now before I go and lock myself up(before someone comes to tear me a new A-hole), I will give some good advice. STAY AWAY OF THESE MIG WELDERS(see pic below)

Notice those two small white switches? Those are your power settings. THEY SUCK!! Either not hot enough, or too hot. When welding panels, you either dont get decent enough penetration in your welds, OR, you burn a f-ing hole through your panel! TRUST ME, I have one gathering dust..... Then, I got me a decent one....

Here you can fine-tune your power settings vs. wire feed. Also, you got a 'timer' option. What this allows you to do is hold down the trigger to do a spot-weld, and after the preset time(in seconds), it will automatically stop welding. So you can for example set it to do a 5 second spot-weld. Much better machine, with WAY better results. I does come at a price though.
Oh yeah, and before I forget. Just as important... Go the extra stretch and get a contract for a gas bottle (normally Argon/CO2 mixture is used, but ATAL is just as good, and cheaper. BUT, it is not recommended to do S.Steel welding with ATAL gas). Forget that Core Flux wire. It SUCKS, especially when welding sheet metal/new panels on your restoration project!!!!!!
Ok, I think it is enough for now playing MR. I-know-it-all !!! And again, BAron, it is not personal, just my take on it

VW Enthusiast








-
- Oil Stain
- Posts: 160
- Joined: Thu Nov 08, 2007 1:07 am
- What model do you have?: Love Bug
- Location: Nazereth, Ethiopia But Stuck in Los Angeles at the moment....
Ohhhh.. You French guys are all the same... You got to remember, this is AFRICA. We dont need no stinking machine... We just plug the cable into the wall and use a coat hanger for an electrode
Welds it right up
Piece of Cake!
No really now. You are 99% correct in all your statements except the part about fluxcore and the fact that you cant weld 10mm steel with TIG .
TIG (in the right hands) will make absolutly the best welds on all types of metals no mater the thickness. To make bigger welds you need a bigger machine. Many people dont know how to weld big welds and will try to weld 2 pieces of 13mm steel together in one pass. [size=18]WRONG! BUT! TIG is a precise process. not a quick process. It requires 2 hands. That is why it is mainly a bench process.
For the typical VW guy the best welder is a MIG welder. If your flux core does not make a good weld, it is because YOU cant weld....[/size]
Another problem here in Africa is that we dont necessarly have a SHOP to work in
Got to work outside or another not quite so desireable place like under the car...
So the gas sheilding wont work worth CACA! Just blows away. And if you are trying to weld something and drink your beer it is very difficult to also hold the part you are welding in place......
One of these days I will figure out how to write and put photos here


No really now. You are 99% correct in all your statements except the part about fluxcore and the fact that you cant weld 10mm steel with TIG .
TIG (in the right hands) will make absolutly the best welds on all types of metals no mater the thickness. To make bigger welds you need a bigger machine. Many people dont know how to weld big welds and will try to weld 2 pieces of 13mm steel together in one pass. [size=18]WRONG! BUT! TIG is a precise process. not a quick process. It requires 2 hands. That is why it is mainly a bench process.
For the typical VW guy the best welder is a MIG welder. If your flux core does not make a good weld, it is because YOU cant weld....[/size]

Another problem here in Africa is that we dont necessarly have a SHOP to work in


One of these days I will figure out how to write and put photos here

MIG/TIG
Hi all,
No offence taken Zero.
The more info we can give the guy the better choice he can make. I agree and disagree with you but lets not go there we are going to highjack the subject.
My statement on penetration dept is based on laboraty samples of weld specimens I see from time to time.
Blitz Im sorry Idid not mention the flux core option, its new technollogy and not known by most by home welders and I dont know how practical it will be ,but its expensive --can be your way out of the bottle situation though.
Dont ignore the oxy/accetalene option---very cheap and very simple to use. The down side --lots of heat distortion ,but that was all the older generation had and with a lot of patoins they build nice cars. JUST CONTROL THE HEAT.
Riftvalleyve you said:- I have some inverter welders that will auto adjust to different voltages and they refuse to work in Ethiopia...well we have the same problem in SA, they allways want more money for less work
cheers
baron
No offence taken Zero.
The more info we can give the guy the better choice he can make. I agree and disagree with you but lets not go there we are going to highjack the subject.
My statement on penetration dept is based on laboraty samples of weld specimens I see from time to time.
Blitz Im sorry Idid not mention the flux core option, its new technollogy and not known by most by home welders and I dont know how practical it will be ,but its expensive --can be your way out of the bottle situation though.
Dont ignore the oxy/accetalene option---very cheap and very simple to use. The down side --lots of heat distortion ,but that was all the older generation had and with a lot of patoins they build nice cars. JUST CONTROL THE HEAT.
Riftvalleyve you said:- I have some inverter welders that will auto adjust to different voltages and they refuse to work in Ethiopia...well we have the same problem in SA, they allways want more money for less work
cheers
baron